Selecting the right abrasive is crucial for achieving the desired finish and efficiency in your woodworking projects. Regardless of the project you’re working on, understanding the different types of abrasives and their applications can save time and improve the quality of your work. Here’s a comprehensive guide to help you choose the best abrasive for your needs.
Factors To Consider When Choosing Abrasives
What Abrasive Type Do I Need?
Aluminum Oxide Abrasives
Aluminum oxide abrasives are some of the most commonly used abrasives due to they versatility and affordability. They’re highly friable, meaning they fragment while cutting, ensuring a consistently sharp cutting surface. However, they have a lower longevity compared to other abrasives, so you’ll need to replace them more often.
Silicon Carbide Abrasives
Silicon carbide abrasives are favoured for finish work due to their even and consistent cut rate. They’re harder and sharper than aluminum oxide, making them more expensive, but their superior cut rate offsets the higher price.
Ceramic Abrasives
Ceramic is a premium abrasive that delivers a continuously sharp cutting surface. It’s one of the most expensive options but offers the longest lifespan, making ceramic abrasives cost-effective for high-volume use.
Zirconia Abrasives
Zirconia abrasives cut aggressively, making them ideal for stock removal in hardwoods and metal grinding or polishing. They’re less expensive than ceramic and have a longevity that falls between aluminum oxide and ceramic.
What Grit Size Do I Need For My Woodworking Project?
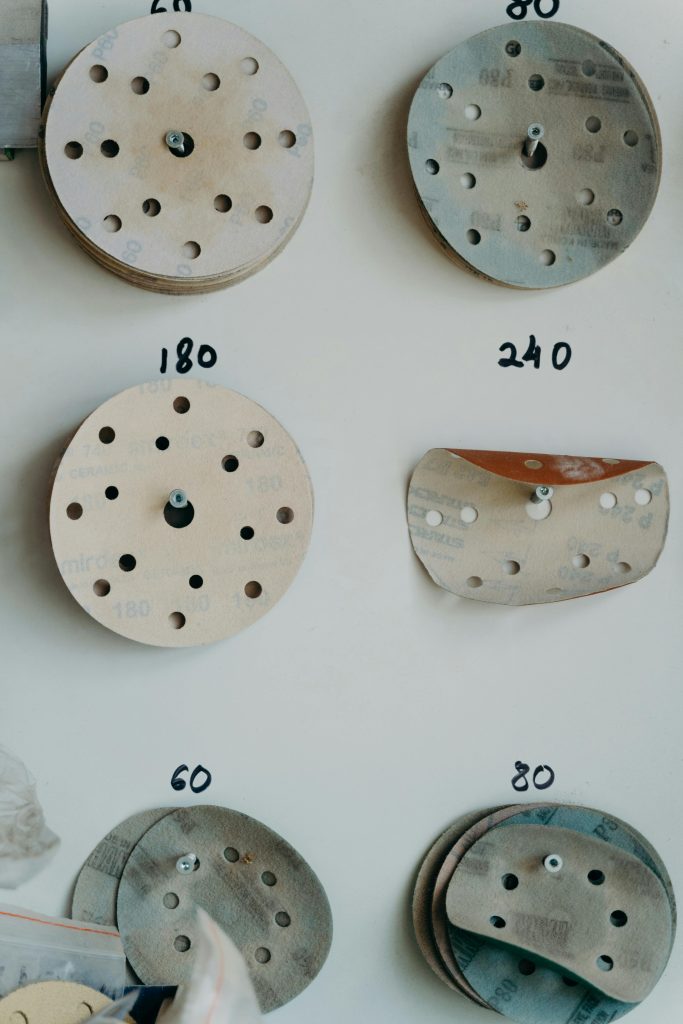
The size of the abrasive particles determines the rate of material removal and the smoothness of the resulting surface. Here’s a quick guide to the different grit ranges:
Coarse Grit (36 to 80):
Best for fast stock removal, such as smoothing the live edge of a slab or sanding down rough-sawn surfaces.
Medium Grit (100 to 180):
Ideal for removing mill marks from machines and preparing a clean surface for finishing.
Fine Grit (220 to 400):
Provides excellent clarity of grain and a smooth surface, often used before the final coat of finish.
Polishing Grit (600 and up):
Used for polishing finished surfaces to achieve a high shine.
Applications Of Different Abrasive Grits
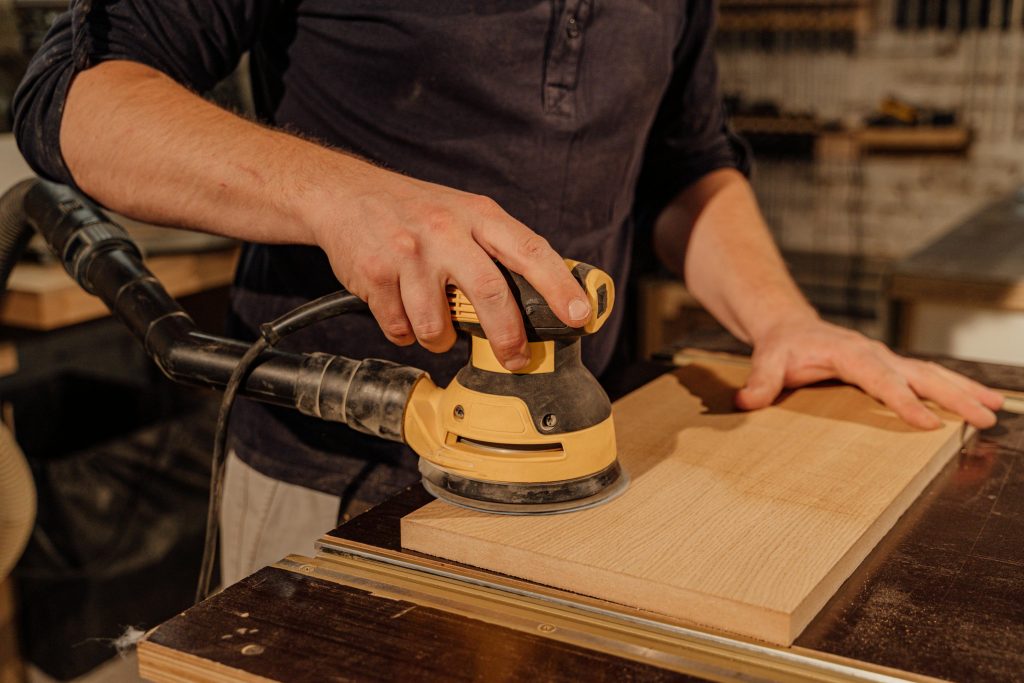
Shaping And Stock Removal
For fast stock removal and shaping, stay in the coarse grit range (36 to 100 grit). This is ideal for tasks like smoothing rough-sawn surfaces or shaping the live edge of a slab.
Paint And Finish Removal
Start with 80 grit for removing old paint or finish, and work your way up to 150 grit for a clean surface ready for refinishing.
Prepping A Surface For Finishing
Use grits between 120 and 220 for prepping surfaces. Sanding by hand or with a power sander at this grit range ensures a smooth surface ready for finishing.
Polishing A Wood Surface After Applying Finish
For polishing, use sandpaper in the 400 to 800 grit range. This helps to smooth out the finish and achieve a high shine.
Backing and Bonding in Abrasives
The abrasive materials are fastened to a backing material. The primary backing materials are paper, cloth, net, plastic film, foam and sponge.
Paper
Paper-backed abrasives are lightweight and cost-effective, ideal for delicate steps like smoothing and polishing. They come in various weights, with heavier papers used for lower grits and lighter papers for fine grits.
Cloth
Cloth-backed abrasives, often made from cotton or polyester, offer strength and flexibility. Polyester backing is waterproof, making it suitable for wet applications.
Net
Net backing allows for dust-free sanding with its unique construction, promoting a clean working environment and excellent cutting performance.
Plastic Film
Plastic film backing provides excellent strength and flexibility. The film can be run with an electrostatic charge, drawing more grit onto the surface. The stronger and flexible edges cause less chatter while sanding as well. It is also water resistant, making it suitable for wet sanding.
Foam And Sponge
Foam and sponge backings are perfect for hand-sanding veneers and moldings, offering the flexibility needed for contoured shapes.
Attaching The Sandpaper To The Sander
Pressure Sensitive Adhesive (PSA) Backing
PSA is widely used commercially where it’s rarely necessary to change to a different grit before the abrasive is worn out. It provides a flat surface and durable adhesive.
Hook And Loop Backing
Hook and loop is commonly used with small hooks on the sanding pad and a soft fabric on the back of the abrasive. This backing creates a light cushion for the pad which can help with any debris on the surface that can leave marks. It also lets some air behind the back of the disc, dissipating heat, which keeps the grit on the pad longer. The hooks on the pad can wear out over time, requiring occasional replacement of the sander pad.
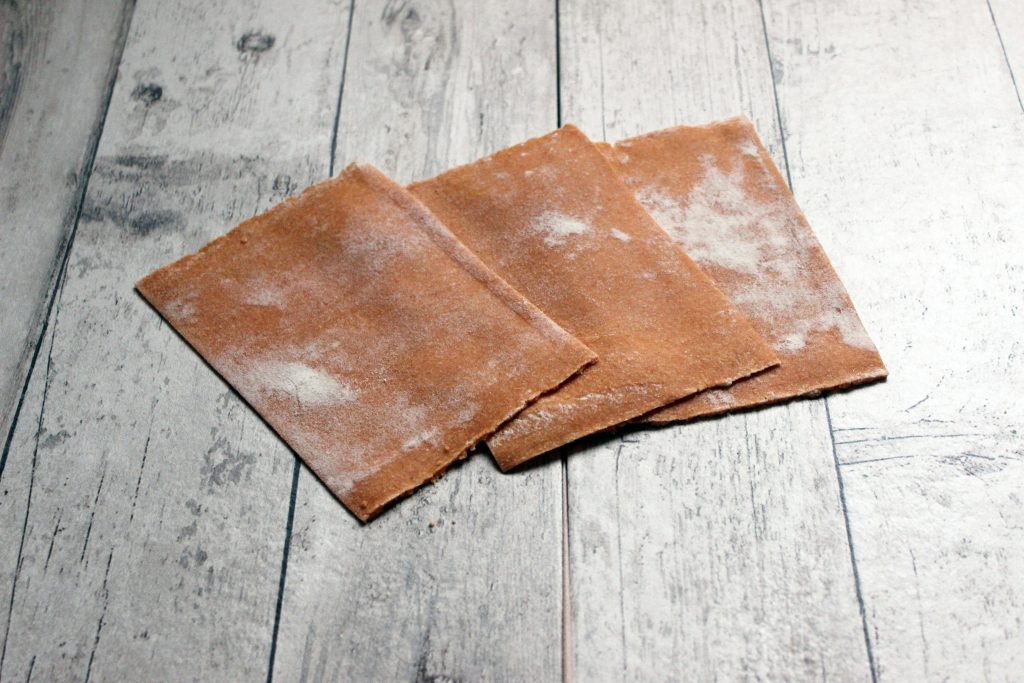
The Perfect Abrasive For Perfect Results
Choosing the right abrasive for your woodworking project can significantly impact the quality and efficiency of your work. By considering the type of abrasive, grit size, backing, and bonding, you can select the best tool for the job. Whether you’re shaping, finishing, or polishing, find the perfect abrasive at McFadden’s today.